
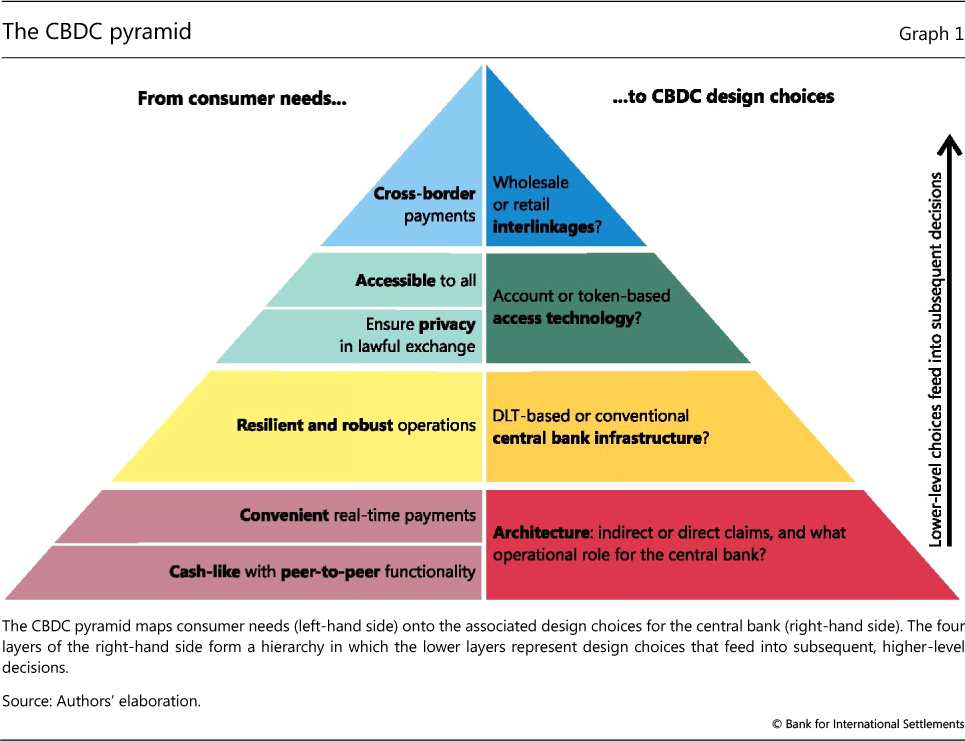
An architectural projects labor costs can be reduced by up to 80% by having most construction completed by 3D printers. 3D printed buildings have much lower building costs than those built with traditional methods because of the reductions in raw material and more importantly labor. Let’s get into the pros and cons of 3D printed construction. While the benefits are endless there are still quite a few hurdles holding back this technology. Less material not only adds to the durability but also saves a ton of money on the construction costs for the architects and contractors using 3D printing. Structures walls are normally hollowed out to allow for utility lines to pass-through and reduce the amount of materials used.
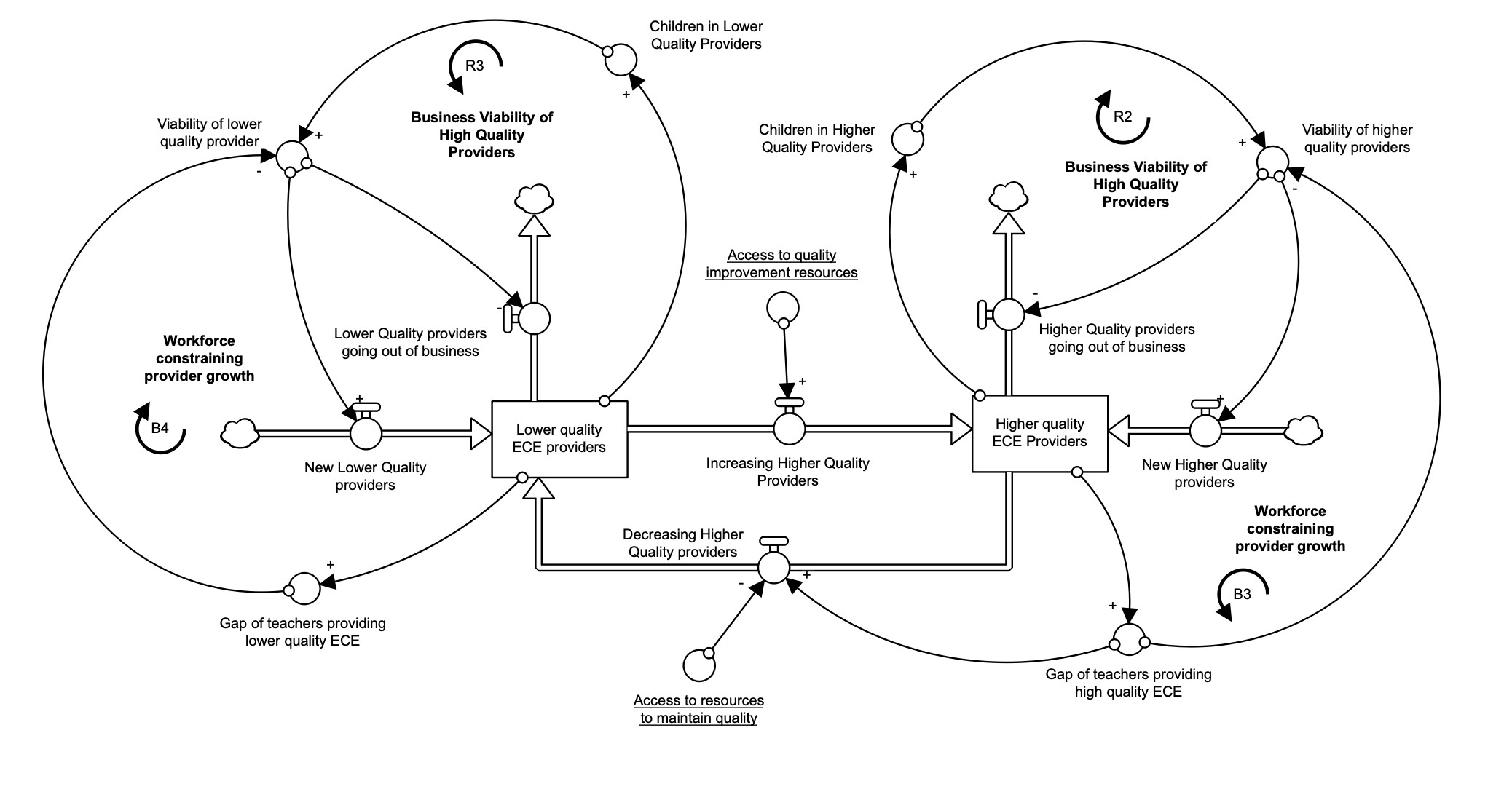
The self-supporting characteristic of 3D printing opens up a whole new realm of possibilities that just are not available with traditional construction methods.ģD printed buildings can easily lay structures using curvilinear forms instead of typical rectilinear forms which makes them a lot more durable. Structures using 3D printing are built with super-sized printers using special cement mixtures that are thicker than concrete so there is no need for support beams. The concept of 3D printing has been around for decades and has had its fair share of ups and downs but seems to be gaining hype once again. Using 3D printing to construct homes or commercial buildings are starting to become a real possibility and are the talk of the town in the AEC industry.
